Why is precision machining vital for rotary airlock valve reliability?
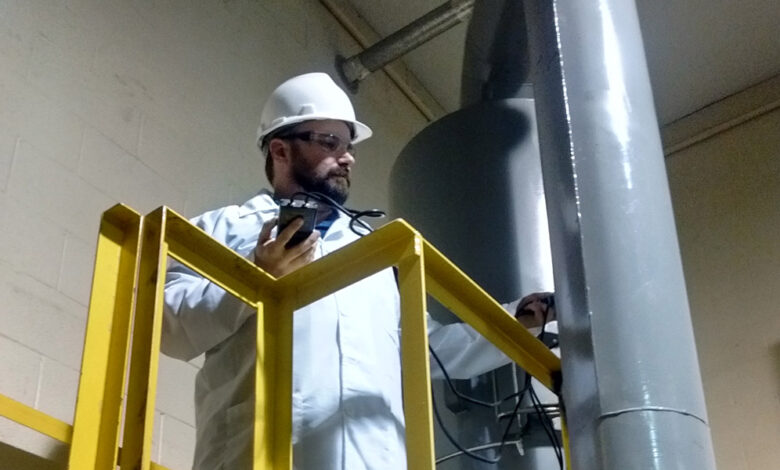
Precision machining stands as the backbone of industrial reliability, transforming raw materials into components that drive complex mechanical systems. Every microscopic detail matters when engineering sophisticated mechanical solutions that must perform consistently under challenging conditions. The intricate world of industrial manufacturing demands absolute accuracy, where even the smallest deviation can compromise the entire system’s performance.
-
Precision engineering
Engineers understand that precision is not merely about meeting dimensional specifications. It represents a comprehensive approach to manufacturing that ensures optimal functionality, longevity, and efficiency. The marriage of advanced technological capabilities with meticulous craftsmanship creates components that can withstand extreme environments and continuous operational stress.
-
Anatomy of a rotary airlock valve
A rotary air lock valve is a critical interface in many industrial processes, managing material flow between different pressure zones. Its primary function involves controlling the movement of bulk materials while maintaining system integrity. The valve must create an effective seal, prevent material leakage, and facilitate smooth material transportation without compromising system pressure differentials.
-
Understanding mechanical complexity
The internal mechanisms of these valves require extraordinary precision. Multiple rotating elements must interact seamlessly, creating tight seals and managing material flow with minimal friction. Each component must be manufactured to extremely tight tolerances, ensuring consistent performance across various industrial applications.
When it comes to rotary airlock valve manufacturing, precision machining becomes paramount. The intricate design demands components that fit together with microscopic tolerance, preventing any potential material leakage or mechanical inefficiencies. Manufacturers invest significant resources in developing machining processes that can produce components meeting exacting specifications.
-
Critical manufacturing considerations
Precision machining techniques incorporate advanced measurement technologies, computer-controlled manufacturing processes, and rigorous quality control mechanisms. These approaches ensure that each rotary airlock valve component meets predetermined performance standards. Sophisticated measurement tools like coordinate measuring machines (CMMs) verify dimensional accuracy down to micrometres.
-
Material selection and machining challenges
Different industrial environments require specific material properties. Precision machining allows engineers to work with various materials – from standard industrial metals to specialized alloys – creating rotary airlock valve components that can withstand extreme temperatures, corrosive environments, and continuous mechanical stress.
-
Engineering resilience through precision
The ability to machine complex geometries with exceptional accuracy means that manufacturers can develop valves capable of performing in diverse industrial sectors. Whether handling cement, food products, chemical compounds, or combustible materials, precision-machined rotary airlock valves ensure consistent, reliable operation.
-
Technological innovations in precision machining
Advanced computational modelling and simulation technologies now complement traditional machining techniques. These tools allow engineers to predict potential performance challenges, optimize design parameters, and reduce manufacturing iterations. Machine learning algorithms help refines machining strategies, pushing the boundaries of what’s possible in component manufacturing.
-
Continuous improvement paradigm
The field of precision machining continues to evolve, driven by technological advancements and increasing industrial demands. Manufacturers consistently invest in research and development, seeking methods to improve machining accuracy, reduce production costs, and enhance overall component reliability.
As technological capabilities expand, so too will our ability to create increasingly sophisticated mechanical solutions that push the boundaries of what’s possible in industrial design. Companies that prioritize precision machining will ultimately distinguish themselves through superior product performance, reduced maintenance requirements, and enhanced operational efficiency.